Statistical Process Control (SPC) is a method of quality control that uses data-driven methods to monitor and control processes in order to ensure they are operating within predetermined limits. The goal of SPC is to optimize process performance in the output of a process.
Implementing SPC requires a thorough understanding of the process, including its inputs and outputs. It also involves identifying and analyzing data on these variables, using statistical tools like control charts. These tools help to track quality and identify areas 5S for improvement improvement from expected goals and objectives.
There are four key components to a process for implementing SPC: Process Quality, Efficiency, Predictability, and Consistency. The first component, Variation, is concerned with the distribution of process data. Each process usually produces a unique signature. Next is Predictability or Capability, which concerns knowing how well the process is working, with the aim of achieving consistency and reliability as close as possible to the expected mean of the industry benchmarks.
The process capability, also known as 'process cpk', measures the center of variation of the process. A target value or a minimum specification and a maximum allowable variation (USL) or a target value or a minimum specification and a lower specification limit defined is required for a process output to operate within these limits and regulations.
A control chart evaluates progress over time and highlights issues and problems in the process. Setting effective monitoring rules includes tracking and trending process performance.
Automated control methods, which include intelligent sensors and data collection systems, offer various tools to optimize and improve process efficiency. These systems usually reduce variability and improve consistency and have become crucial in high-volume production.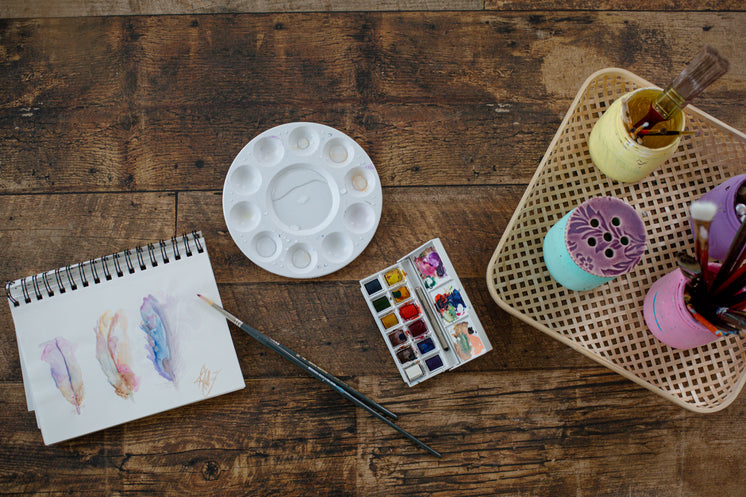
Implementing SPC requires a thorough understanding of the process, including its inputs and outputs. It also involves identifying and analyzing data on these variables, using statistical tools like control charts. These tools help to track quality and identify areas 5S for improvement improvement from expected goals and objectives.
There are four key components to a process for implementing SPC: Process Quality, Efficiency, Predictability, and Consistency. The first component, Variation, is concerned with the distribution of process data. Each process usually produces a unique signature. Next is Predictability or Capability, which concerns knowing how well the process is working, with the aim of achieving consistency and reliability as close as possible to the expected mean of the industry benchmarks.
The process capability, also known as 'process cpk', measures the center of variation of the process. A target value or a minimum specification and a maximum allowable variation (USL) or a target value or a minimum specification and a lower specification limit defined is required for a process output to operate within these limits and regulations.
A control chart evaluates progress over time and highlights issues and problems in the process. Setting effective monitoring rules includes tracking and trending process performance.
Automated control methods, which include intelligent sensors and data collection systems, offer various tools to optimize and improve process efficiency. These systems usually reduce variability and improve consistency and have become crucial in high-volume production.
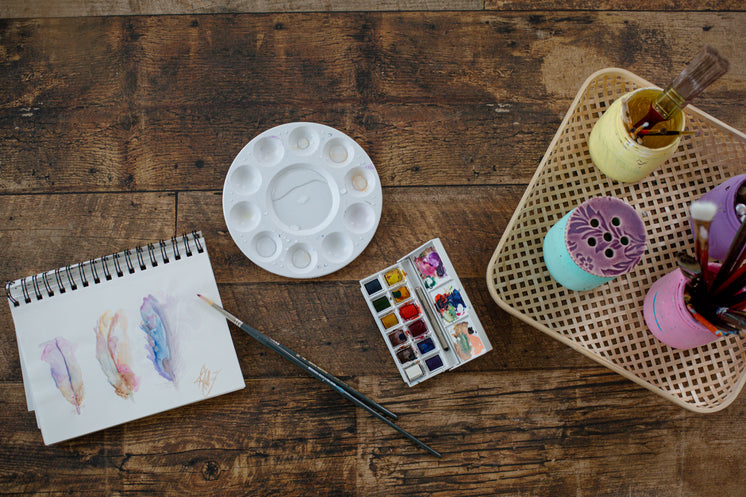
댓글 달기 WYSIWYG 사용